(1) When used with multi-axis servo body-in-white positioning technology, the workpiece realizes the "height 0 transport" (the body is highly consistent in operation and transport status) mode to improve stability and transport efficiency;
(2) When the width of different vehicle bodies is different, the pneumatic servo structure developed by the company is used to realize flexible collinearity of multiple vehicle types.
Uniqueness:
Breakthrough:
(1) Compared with the traditional roller bed equipment, the mechanism is simple and the conveying efficiency is high. The precision matching formed by the servo technology combined with the gear rack greatly improves the production efficiency of the line body;
(2) Using servo synchronization technology and transmission structure optimization design, the transmission speed is greatly improved.
(2) Using servo synchronization technology and transmission structure optimization design, the transmission speed is greatly improved.
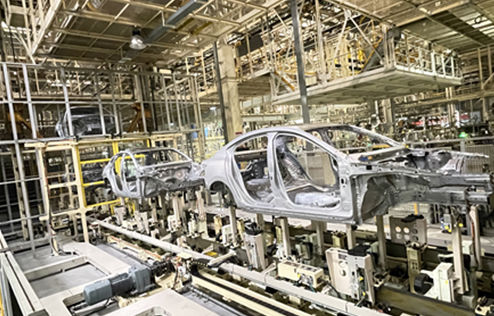